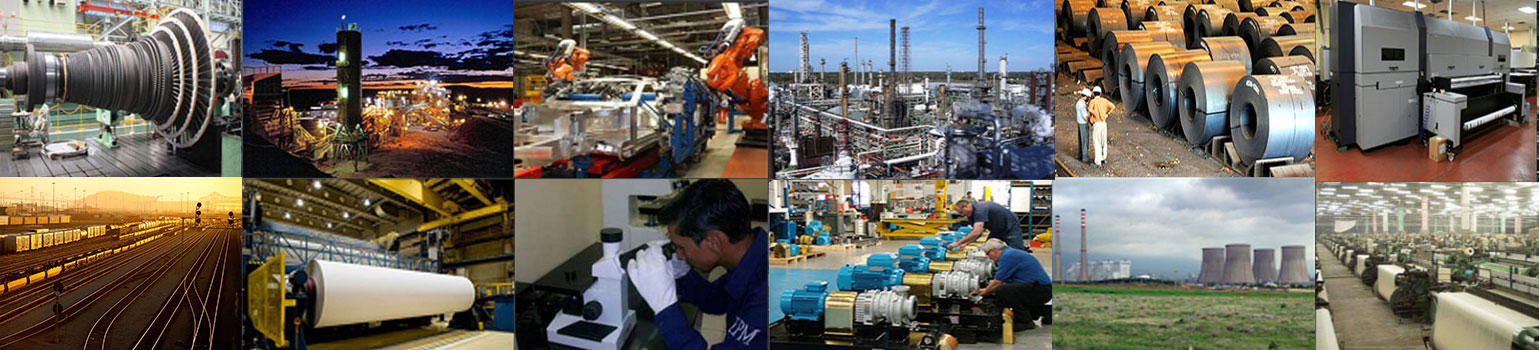
Surface Modification- FAQs
FAQ 1 : What is Thermal Spray and what are its advantages?
Thermal spraying techniques are coating processes in which melted or heated materials are sprayed onto a surface.
Coating materials available for thermal spraying include metals, alloys, ceramics, plastics and composites. They are fed in powder or wire form, heated to a molten or semi-molten state and accelerated towards substrates in the form of micrometer-size particles. Combustion or electrical arc discharge is usually used as the source of energy for thermal spraying. Resulting coatings are made by the accumulation of numerous sprayed particles.
IPM provides international quality thermal spray coatings along with other crucial surface modification services.
The advantages of these services include-
- cold process, no risk of distortion or change in properties of the parent material
- the surface becomes ‘Ultra Hard’
- highly corrosion, erosion, abrasion and wear resistant
- enhanced life of the components
- reduced down time for the concerned workshop
Thermal spray can also be used in repair procedures to restore components to their original dimensions. The coatings can be ground to finished size. These services are carried out at IPM using latest robots and microprocessor controlled equipment.
FAQ 2 : What are the types of thermal spray processes available and which one is the best?
Some of the thermal spray processes available at IPM include:
- High Energy Plasma spraying
- Combustion Flame spraying
- High Velocity Arc Spray
- High Velocity Oxy-Fuel spray (HVOF)
- High Pressure High Velocity Oxy-Fuel spray (HP-HVOF)
The type of process depends on the component and its properties as well as the quality and performance desired by the customer. In case of specific queries, please feel free to contact us and we will be happy to study your specific case and suggest a process that is most beneficial for your components.
FAQ 3 : How is the quality of the coating assessed?
Coating quality is assessed by measuring its porosity, oxide content, micro-hardness, bond strength and surface roughness. The comprehensive in-house testing laboratory at IPM ensures that the coating is of the highest quality.